New software improves accuracy of factories’ mass-produced 3D-printed parts
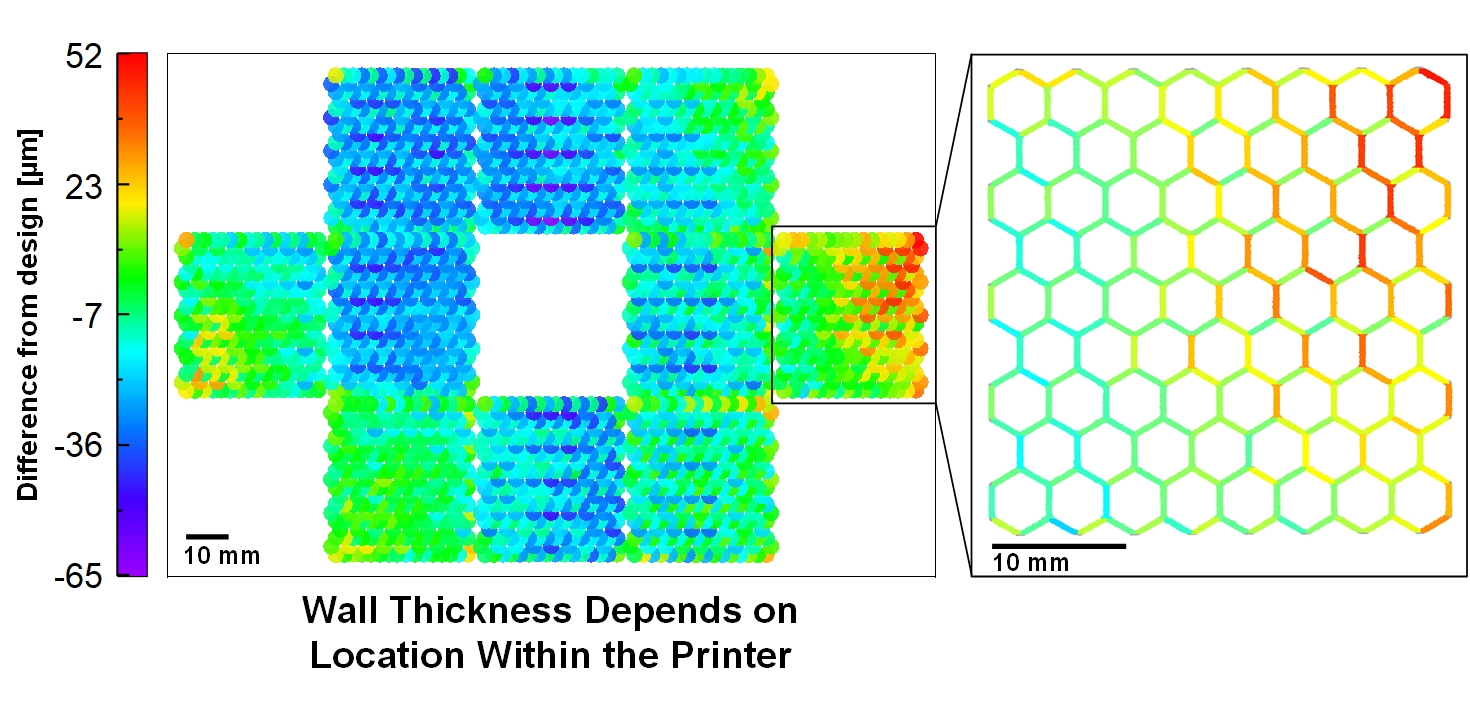
Analyzing part accuracy and sources of variability for additively manufactured lattice parts made on multiple printers
has been accepted to Additive Manufacturing.
- We propose a framework for analyzing additive manufacturing variability.
- Statistical modeling analyzes accuracy for parts made on multiple printers.
- Part accuracy varies for different printers even when all other parameters are constant.
- A generalized linear model can predict part accuracy.
Press Release
-By University of Illinois Urbana-Champaign
Researchers at University of Illinois Urbana-Champaign developed software to improve the accuracy of 3D-printed parts, seeking to reduce costs and waste for companies using additive manufacturing to mass produce parts in factories.
“Additive manufacturing is incredibly exciting and offers tremendous benefits, but consistency and accuracy on mass-produced 3D-printed parts can be an issue. As with any production technology, parts built should be as close to identical as possible, whether it is 10 parts or 10 million,” said Professor Bill King, Andersen Chair in the Department of Mechanical Science and Engineering and leader of the project.
The team’s software allows for the rapid and automatic measurement of additively manufactured parts – a processes that is typically time consuming and costly. It also allows for increased accuracy.
“Factories that rely on 3D printing are being built rapidly all over the world. Our software helps ensure production is consistent, accurate, and cost-effective,” King said.
The software tracks how the accuracy of an additively manufactured part depends on which printer made the part and where the part was located in the printer. This process works by measuring parts using optical scanning technology and analysis of the scan data. This analysis allows a user to determine which parts are accurate and identifies which printers, and settings, produce the most accurate parts.
The University of Illinois researchers collaborated with engineers at Fast Radius Inc., a Chicago-based company with one of the world’s largest additive manufacturing factories. In 2018, the World Economic Forum identified Fast Radius as one of the world’s most advanced digital factories. King is one of the company’s co-founders and serves as its chief scientist.
The research was published this month in Additive Manufacturing, in an article titled: “Analyzing part accuracy and sources of variability for additively manufactured lattice parts made on multiple printers.” Authors on the study are Davis J. McGregor, Sameh Tawfick, and Chenhui Shao, and William King from University of Illinois, and Samuel Rylowicz, Aaron Brenzel, Daniel Baker, Charles Wood, David Pick, and Hallee Deutchman from Fast Radius.
Abstract
Scalable production using additive manufacturing (AM) requires quality systems that monitor and control manufacturing variability across many machines in a factory environment. AM process variability can result in geometric inaccuracies in parts that can affect their mechanical behavior; however, most research focuses on a single machine and hardware set, while part inaccuracy and AM variability across multiple printers remains poorly understood. This study establishes a framework to study the accuracy of polymer parts made on three identical printers and evaluates the role of manufacturing process parameters and their impact on part variability. We fabricate 90 polymer hexagonal lattice parts over nine builds on three identical Carbon M2 machines with interchangeable hardware tools. Each part is measured using automated metrology that extracts the size and shape of the part features and automatically measures defects. Each hexagonal part consists of 237 individual walls that were measured for 90 parts, resulting in 21,330 individual geometric measurements. Using statistical methods to analyze geometric defects as a function of machine, hardware set, and location in the build, we find that the observed variability can be correlated with process parameters. Geometric defects in the wall thickness depend upon machine and location within the build but do not depend on the hardware tool, while geometric defects in the wall length and height of the part depend upon machine and tool but not location. The uniformity within the parts, measured by standard deviations of the individual features within a part, mostly depends upon unmeasured parameters. We use a generalized linear model (GLM) to model the variability and to predict defects. The framework introduced here can be extended to analyze additional machines and process parameters and provides a practical tool to account for manufacturing variability in an AM production environment.
UIUC Press Release News Mention
Related LinkedIn Post
Related Tweets
#ILLINOIS researchers developed a software that improves the accuracy of 3D-printed parts mass produced in factories.
— The Grainger College of Engineering (@uofigrainger) March 18, 2021
This innovation could reduce cost and waste for companies using additive manufacturing 🔸 https://t.co/PtjmSHG9ca pic.twitter.com/JmOxxCNPIz